What are the operating procedures for the molding machine!
Time:2024-02-20
Views:385
What are the operating procedures for the molding machine? Here is an introduction to the operating procedures of the shaping machine for your reference:
Start up procedure for the molding machine
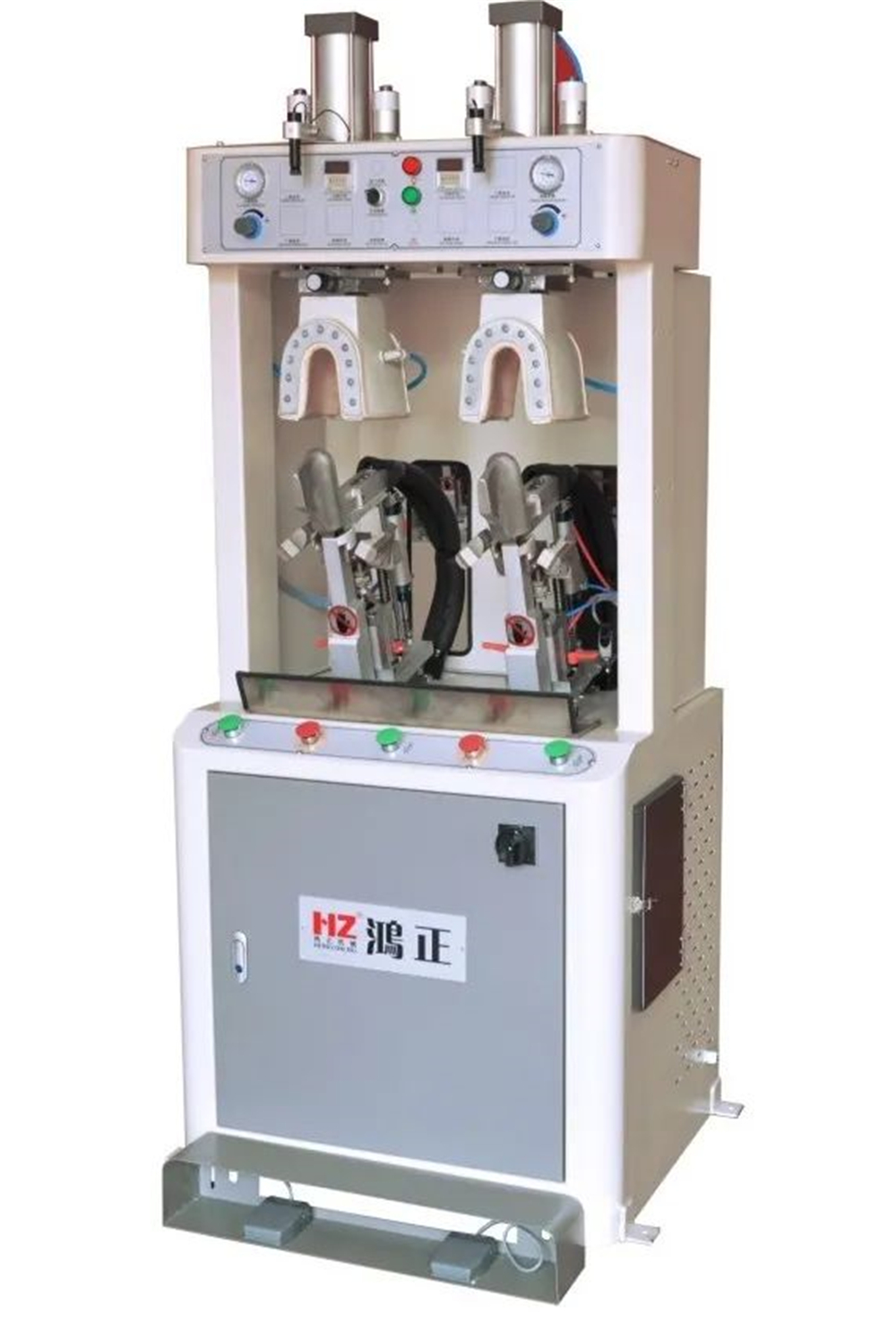
1. Click the feeding mechanism button of the molding machine to enter the feeding mechanism operation interface, and click the feeding main control switch in the upper left corner to turn red
2. Click the dispensing mechanism button of the molding machine to enter the dispensing mechanism operation interface, and click the dispensing main control switch in the upper left corner to turn red.
3. Press the reset button "RESET" on the operation panel, the indicator light will turn off, the startup indicator light will flash, press the startup indicator light, the chain will rotate, and the acceleration indicator light will flash.
4. Click the oven button to enter the heating system:
a. Click on the schematic icon of the circulating fan to enter the power setting window of the circulating fan. Click on the total button of the circulating fan to pop up the power setting window of the circulating fan. Click on the white bottom number box to pop up the numeric keypad, enter the required output power value, and press confirm.
b. Click on the schematic icon of the exhaust fan in the upper left or upper right corner to enter the exhaust fan power setting window, click on the manual control button and confirm, click on the white background number box to pop up a small numeric keypad to enter the required value and confirm. If you click the automatic control button and confirm, the exhaust fan will automatically adjust the power of the exhaust fan.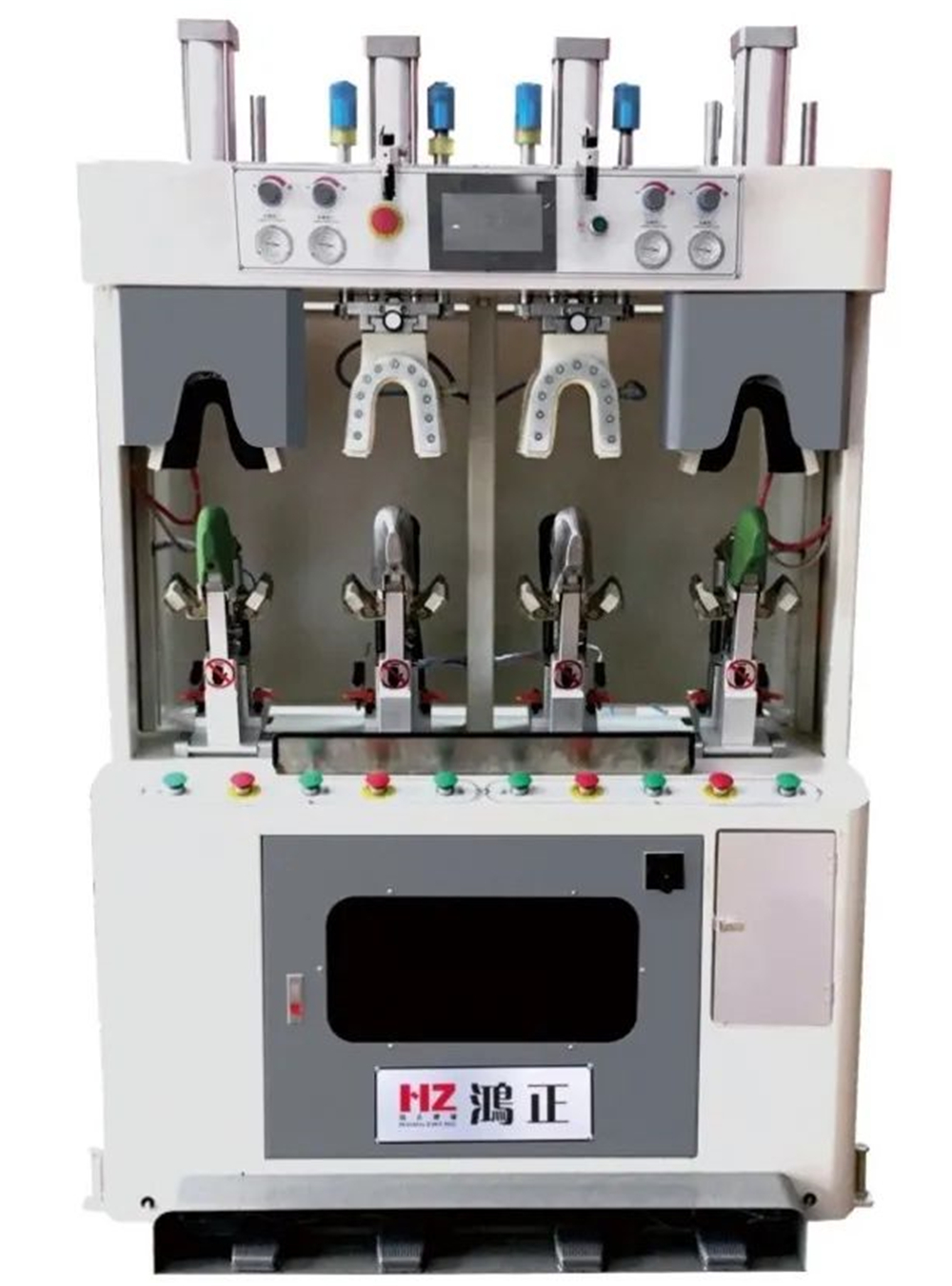
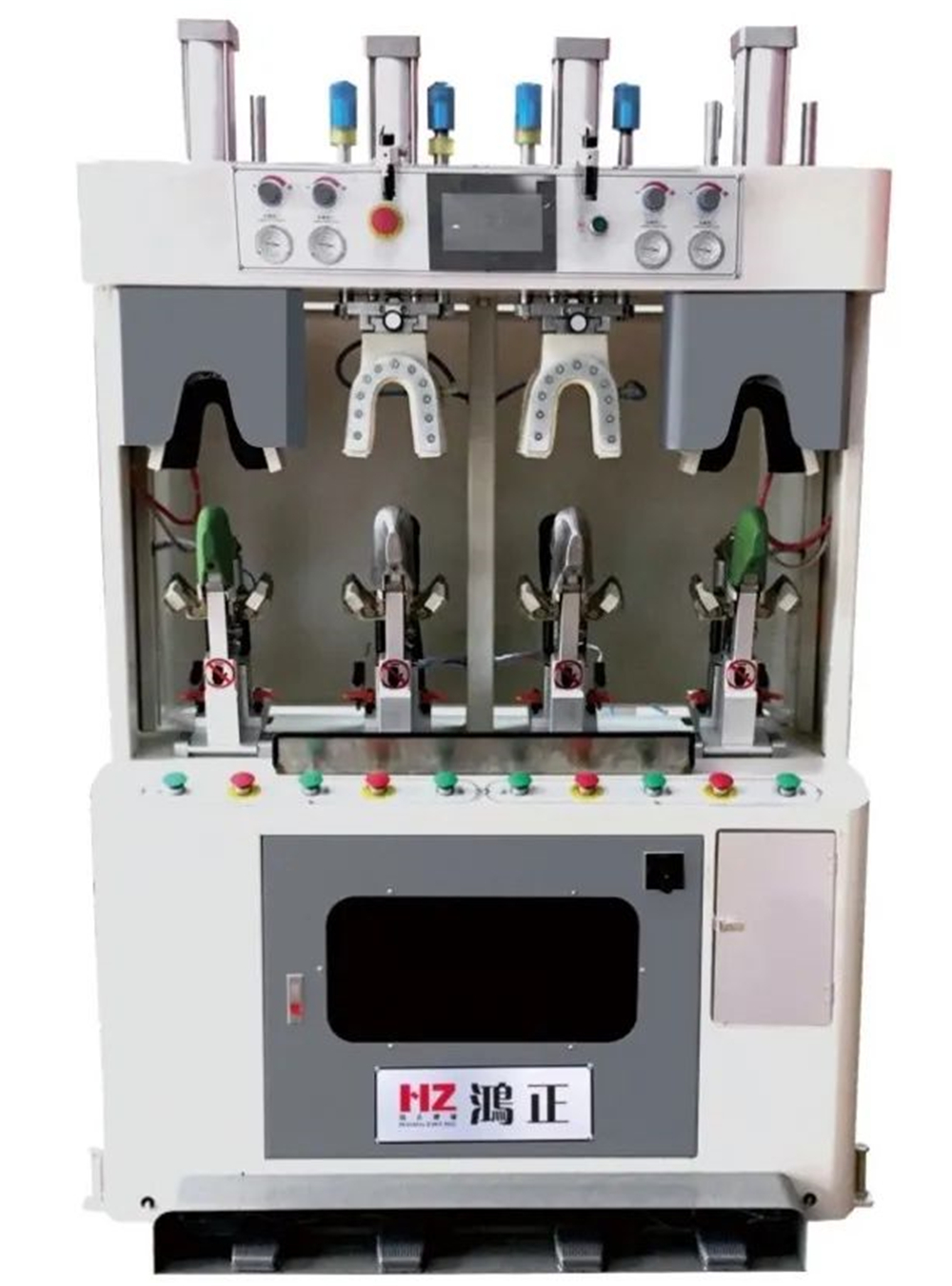
Click on the numerical box displaying temperature in the oven simulation icon to enter the heating window. Click on the heating total to set the heating temperature, or you can set the heating temperature for each section of the oven separately. When the heating temperature is below 90 degrees, click on the low fire icon for heating. When the heating temperature is above 90 degrees, click on the high fire icon for heating and confirm.
5. The correct threading route is to thread the fabric guide 9 into the feeding section from the feeding frame to the operating table, and to thread the fabric guide belt out of the feeding section along the correct threading route (from the feeding roller to the feeding frame).
6. The red shutdown button on the lower operation panel stops the chain operation and the startup indicator light flashes. Guide the fabric up the tension chain and press the down button of the overfeed wheel for about 10 seconds, until the indicator light of the down button lights up. Turn on the motors of each part of the feeding mechanism to "1". Raise the slurry pouring tank, apply the rolling mill pressure, turn on the motors in all parts of the operating table (except for the needle protection inlet button), and click the feeding control button in the upper left corner of the feeding mechanism until it turns green.
7. Start the front half of the machine and wait for the fabric to pass through the needle protection entrance. Then turn on the needle protection entrance button to "1". Stop the machine when the fabric is discharged from the oven and reaches the feeding roller. Connect the fabric to the guide belt of the discharge section. Click on the main control button of the feeding mechanism to green, turn on the motors of the feeding section to "1" (except for the tension motor switch of the cooling cylinder), restart the machine, guide the fabric into the feeding frame, and then stop. Turn on the tension motor switch of the cooling cylinder to "1".
8. Click on the stretching chain control button of the molding machine to enter the chain control interface. According to the process requirements on the process card, input the width and confirm it
9. According to the process card, find the fabric to be processed and push it to the feeding point. Connect the guide fabric, prepare the chemical material, and place it in the pouring tank (discharge the first 20L). According to the organization and process requirements of the fabric to be processed, it can be rolled or loaded onto a vehicle. Set parameters for each part and preset according to the weft inclination of the fabric to be processed
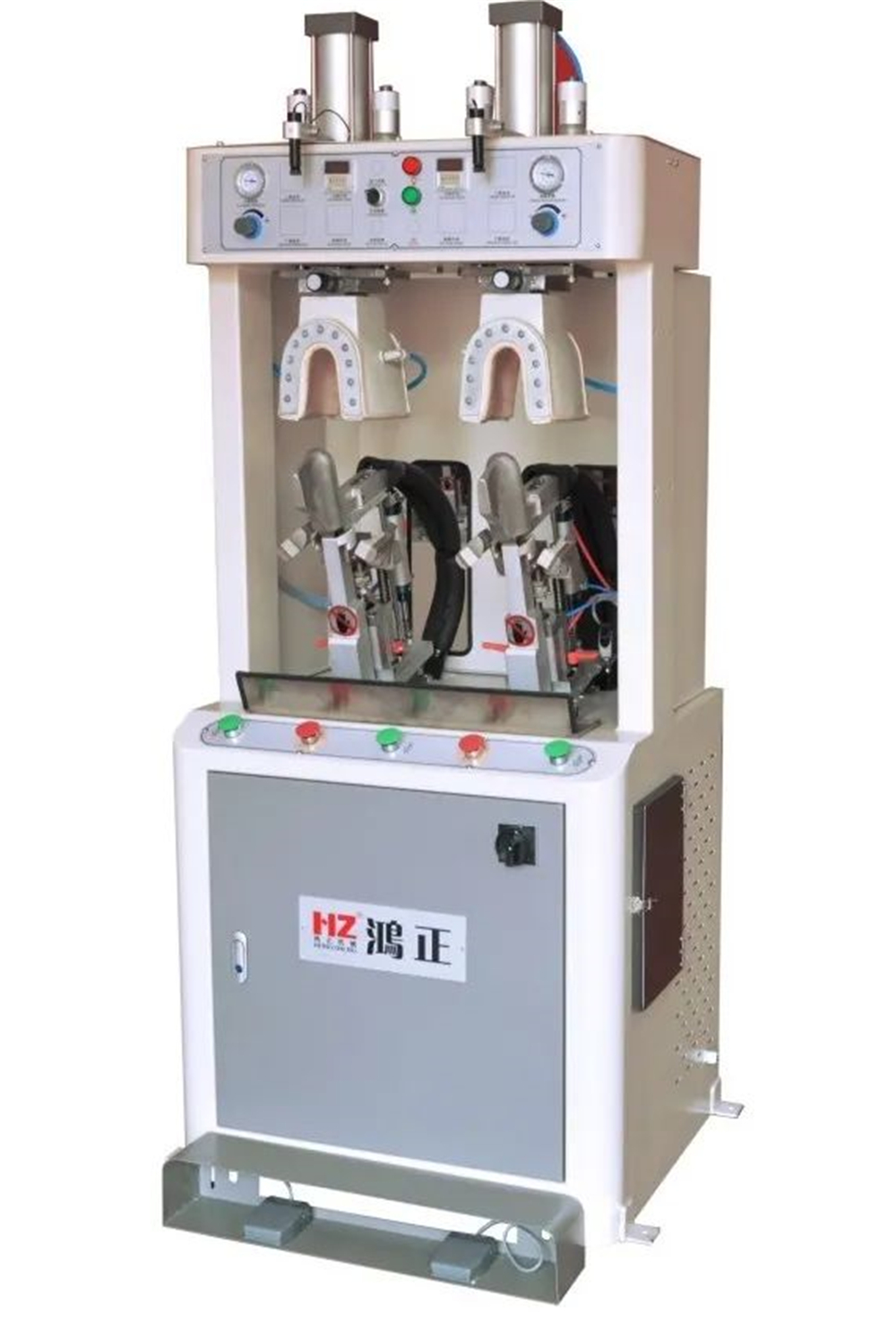